Bearing Trivia
Oil Seals (Part 2): How to select the right oil seal
- #4 Oil Seals
In Part 1, we explained the structure, functions, and types of oil seals.
Oil Seals (Part 1): The structure, functions, and types of oil seals
Oil seals come in various shapes to fit the machines and substances to be sealed.
For this reason, when designing a machine, it is important to select the oil seal that is right for that machine.
That's where this column comes in.
We will explain the key points for selecting the oil seal that is right for your machine.
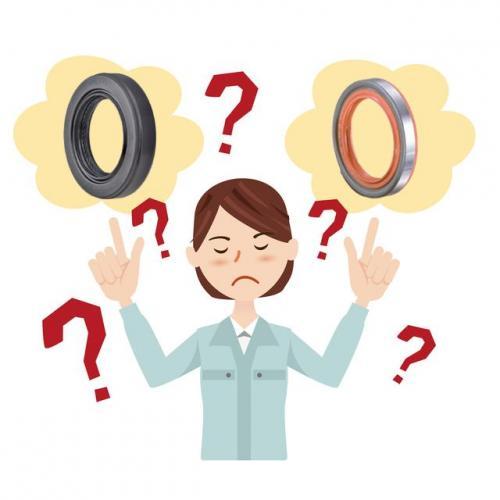
1. Criteria for selecting oil seals
Oil seals come in a wide range of types, and they also have various sizes.
When selecting the right oil seal for your machine from among these many varied types of oil seals, the following two criteria are very important.
- Criterion 1: It should be appropriate for the machine's usage environment and the operating condition that is being demanded of the oil seal
- Criterion 2: It should be easy to acquire replacement oil seals and it should facilitate maintenance/inspection of the machine
If these criteria are met, damage of the machine can be reduced, the time needed to replace the oil seals when performing repairs can be shortened, and the machine can be used for a longer period of time.
In this way, selecting the appropriate oil seal will lead to machine design that is economically superior!
2. How to select the right oil seal
In general, oil seals should be selected in the order of priority indicated in Table 1.
However, when you actually select the oil seal to use, the most important factors are past success history and points of improvement, so it is not necessary to follow this order to the letter.
Table 1: The order of priority for selecting oil seals
No. | Examination item |
1 | Seal type |
2 | Rubber material |
3 | Metal case and spring material |
1) Seal type
Select your oil seal type according to Table 2.
Table 2: How to select the seal type
No. | Examination item | Flowcharts |
1 | O.D. (outside diameter) wall material | Figure 1 |
2 | Necessity of spring | Figure 2 |
3 | Lip type | Figure 3 |
Figure 1: O.D. (outside diameter) wall material
Figure 2: Necessity of spring
Figure 3: Lip type
<Seal selection example>
Based on the above flowcharts, the oil seal type that meets the requirements shown in Table 3 would be the type code MHSA or HMSA shown in Table 4.
Table 3: Requirements
No. | Requirements | |
1 | Housing | Made of steel, one solid design, housing bore surface roughness 1.8 μmRa |
2 | Substance to be sealed | Grease |
3 | Pressure | Atmospheric |
4 |
Shaft surface speed (peripheral speed) |
6 m/s |
5 | Air-side condition | Dusty |
Table 4: Type of selected seal
Type 1 | Type 2 | |
O.D. wall material | Rubber O.D. wall | Metal O.D. wall |
Necessity of spring | Spring required | Spring required |
Lip shape | Minor lip required | Minor lip required |
Type (type code) |
![]() |
![]() |
For a more detailed discussion of seal types and type codes, please see the following:
2) Rubber material
The rubber material used in the oil seal should be selected based on the operational temperature and substance to be sealed.
Table 5 lists the major rubber materials along with their operational temperature ranges.
Note that it is necessary to check the compatibility with fluids.
<N.B.>
Extreme pressure additives are compounds added to the lubricant. They are activated by heat and chemically react against rubber, which deteriorates rubber properties. For this reason, it is necessary to check for compatibility with rubber materials.
Table 5: Major rubber materials and their operational temperature ranges
Rubber material (ASTM*1 code) |
Grade | Features | Operational temperature range (°C) | Compatibility with fluids |
Nitrile rubber (NBR) |
Standard type |
Well-balanced in terms of resistance to abrasion and high and low temperatures |
-30~100 |
Necessary to check compatibility with fluids Fluids |
High- and low-temperature-resistant type | Highly resistant to both high and low temperatures | -40~110 | ||
Hydrogenated nitrile rubber (HNBR) |
Standard type |
Compared with nitrile rubber, superior in resistance to heat and abrasion |
-30~140 | |
Acrylic rubber (ACM) |
Standard type | High oil resistance and good abrasion resistance | -20~150 | |
High- and low-temperature-resistant type | Improved low temperature resistance and same level of heat resistance as the standard type | -30~150 | ||
Silicone rubber (VMQ) |
Standard type | Wide operational temperature range and good abrasion resistance | -50~170 | |
Fluoro rubber (FKM) |
Standard type | The most superior in resistance to heat, and good abrasion resistance | -20~180 |
Notes
*1 ASTM: American Society for Testing and Materials
*2 For more details on fluid compatibility, please see the following:
Rubber materials, operational temperature ranges and their compatibility with fluids
3) Metal case and spring material
The metal case and spring material used in the oil seal should be selected based on the substance to be sealed.
Table 6 shows how to select the metal case and spring materials.
Table 6: Selection of metal case and spring materials
Substance to be sealed | Material | |||
Metal case | Spring | |||
Cold rolled carbon steel sheet |
Stainless steel sheet |
High carbon steel wire |
Stainless steel wire (JIS* SUS304) |
|
Oil | ○ | ― | ○ | ― |
Grease | ○ | ― | ○ | ― |
Water | × | ○ | × | ○ |
Seawater | × | × | ○ | |
Water vapor | × | ○ | × | ○ |
Chemicals | × | ○ | × | ○ |
Organic solvent | ○ | ○ | ○ | ○ |
Notes
* JIS: Japanese Industrial Standard
✓: Compatible
✗: Incompatible
―: Not applicable
3. Shaft and housing design
Oil seals can show good sealing performance in combination with properly designed shafts and housings.
1) Shaft design
Table 7 shows the shaft design checklist.
Table 7: Shaft design checklist
No. | Examination item | Major points to confirm | Remarks |
1 | Material | Use one of the carbon steels for machine structural use, low-alloy steel, or stainless steel. | Soft materials (brass and so on) are not suitable. |
2 | Hardness | Shaft hardness should be at least 30 HRC. In usage conditions where wear can occur easily because of dust or contaminated oil, hardness should be 50-60 HRC. | |
3 | Shaft diameter tolerance | This should be h8 (seals are designed to suit shafts with a tolerance of h8). | |
4 | Shaft end chamfer | "Provide a chamfer on the shaft end. (This prevents failure during mounting.)" |
See Figure 4. |
5 | Surface roughness and finishing | The shaft surface to be in contact with the lip should be finished to 0.1 to 0.32 μmRa and 0.8 to 2.5 μmRz and the lead angle to no greater than 0.05°. (There is a risk that the lead marks will impede the sealing performance of the oil seal: see Figure 5.) |
Nominal shaft diameter d1, mm |
d1-d2, mm | |
を超え | 以下 | |
― | 10 | 1.5 min. |
10 | 20 | 2.0 min. |
20 | 30 | 2.5 min. |
Figure 4: Shaft end chamfer
![]() |
![]() |
a) Good finished surface (no lead marks) |
b) Undesirable finished surface (visible lead marks) |
Figure 5: Shaft surface with and without lead marks
2) Housing design
Table 8 shows the housing design checklist.
Table 8: Housing design checklist
No. | Examination item | Major points to confirm | Remarks |
Material | Steel or cast iron is generally used as the housing material. Aluminum alloys and resin (materials with a large difference between the linear expansion coefficients) demand sufficient consideration (as there is a risk of failure due to the increased clearance with the oil seal at high temperatures). |
||
2 | Bore diameter tolerance | 1. If the nominal bore diameter is 400 mm or less: H7 or H8 2. If the nominal bore diameter exceeds 400 mm: H7 |
|
3 | Bore inlet chamfer | Provide an appropriate chamfer with rounded corners. (This facilitates mounting.) |
See Figure 6. |
4 | Shoulder diameter (if the housing bore has a shoulder) |
Set appropriate shoulder diameter. | See Figure 7. |
5 | Bore surface roughness | 1. For metal O.D. wall type: 0.4 to 1.6 μmRa, 1.6 to 6.3 μmRz 2. For rubber O.D. wall type: 1.6 to 3.2 μmRa, 6.3 to 12.5 μmRz (Firmly affixes the oil seal and prevents leakage through the seal O.D.) |
Nominal seal width |
B1 min. mm |
L mm |
|
Over | Up to | ||
― | 10 | b + 0.5 | 1.0 |
10 | 18 | 1.5 | |
18 | 50 | b + 0.8 |
Figure 6: Recommended housing bore chamfers (shouldered bore)
Nominal seal O.D. |
F mm |
|
Over | Up to | |
― | 10 | D - 4 |
10 | 18 | D - 6 |
18 | 50 | D - 8 |
Figure 7: Recommended housing shoulder diameters
3) Total eccentricity
When the total eccentricity is excessive, the sealing edge of the seal lip cannot accommodate shaft motions and leakage may occur.
Total eccentricity is the sum of shaft runout and the housing-bore eccentricity.
Total eccentricity, shaft runout and housing-bore eccentricity are generally expressed in TIR (Total Indicator Reading).
A) Shaft runout
As shown in Figure 8, shaft runout is defined as being twice the eccentricity between the shaft center and center of shaft-center rotation trajectory.
Figure 8: Shaft runout
B) Housing-bore eccentricity
As shown in Figure 9, housing-bore eccentricity is defined as being twice the eccentricity between the housing-bore center and shaft rotation center.
Figure 9: Housing-bore eccentricity
4) Allowable total eccentricity
The allowable total eccentricity is the maximum total eccentricity at which the sealing edge can accommodate shaft rotation and retain adequate sealing performance. The oil seal's allowable total eccentricity is affected by the design of the oil seal, the accuracy of the shaft, and the operating conditions.
For details on shaft and housing design, please see the following:
Examples of allowable total eccentricity for oil seals
4. Seal characteristics
Oil seal performance is affected by not only the type and material of the selected oil seal, but also a variety of other factors, such as operating conditions, total eccentricity, rotational speed, the substance to be sealed, and lubrication conditions.
Figure 9 shows items relating to oil seal characteristics.
Figure 9: Items relating to oil seal characteristics
No. | Item | Content | Major factors |
1 | Sealing property | Lip pumped volume (the volume of oil, etc., pushed back at the lip contact area per unit of time) |
• Shape (hydrodynamic ribs) • Rotational speed • Oil viscosity, etc. |
2 | Oil seal service life | Wear on the rubber material Loss of lip sealing function |
• Operational temperature • Total eccentricity • Rotational speed • Substance to be sealed • Lubrication conditions, etc. |
3 | Lip temperature | Temperature rise due to sealing edge friction heat because of the shaft rotation | • Rotational speed, etc. |
4 | Allowable peripheral speed | When shaft rotation is extremely fast, the sealing performance deteriorates. | • Total eccentricity • Rubber material • Seal type, etc. |
5 | Allowable internal pressure | Internal pressure is a factor that may deteriorate seal performance. | • Total eccentricity, etc. |
6 | Seal torque | The seal torque is large. | • Lip radial load • Lubricating oil • Rotational speed • Shaft diameter, etc. |
For a more detailed discussion of seal characteristics, please see the following:
Seal characteristics
5. Conclusion
When selecting the oil seal that is right for your machine, it is important that the oil seal be appropriate for the requirements of the usage environment and that it be easily acquired for replacement.
In this month's column, "How to select the right oil seal," we conveyed the following points:
1) Oil seal shape and material should be selected based on the housing, substance to be sealed, pressure, rotational speed, total eccentricity, and air-side conditions.
2) Oil seals can show good sealing performance in combination with properly designed shafts and housings.
3) Oil seal performance is affected by not only the type and material of the selected oil seal, but also a variety of other factors, such as operating conditions, total eccentricity, rotational speed, the substance to be sealed, and lubrication conditions. For this reason, diligent care is required in oil seal selection.
In order for the sealing property of the oil seal you selected to really shine, attention needs to be paid to how it is handled.
In the event of seal failure, it is necessary to take effective countermeasures.
We will cover these points in the next column, "Oil Seals (Part 3)".
If you have any technical questions regarding oil seals, or opinions/thoughts on these "Bearing Trivia" pages, please feel free to contact us using the following form: