In selecting the proper fit, careful consideration should be given to bearing operating conditions.
Major specific considerations are :
- Load characteristics and magnitude
- Temperature distribution in operating
- Bearing internal clearance
- Surface finish, material and thickness of shaft and housing
- Mounting and dismounting methods
- Necessity to compensate for shaft thermal expansion at the fitting surface
- Bearing type and size
In view of these considerations, the following paragraphs explain the details of the important factors in fit selection.
1) Load characteristics
Load characteristics are classified into three types : rotating inner ring load; rotating outer ring load and indeterminate direction load.
Table 9-1 tabulates the relationship between these characteristics and fit.
Table 9-1 Load characteristics and fits
Rotation pattern | Direction of load | Loading conditions | Fit | Typical application | |
---|---|---|---|---|---|
Inner ring & shaft | Outer ring & housing | ||||
![]() |
![]() |
Rotating inner ring load Stationary outer ring load |
Interference fit necessary (k、m、n、p、r) |
Clearance fit acceptable (F、G、H、JS) |
Spur gear boxes, motors |
![]() |
![]() |
Greatly unbalanced wheels | |||
![]() |
![]() |
Stationary inner ring load Rotating outer ring load |
Clearance fit acceptable (f、g、h、js) |
Interference fit necessary (K、M、N、P) |
Running wheels & pulleys with stationary shaft |
![]() |
![]() |
Shaker screens (unbalanced vibration) | |||
Indeterminate | Rotating or stationary | Indeterminate direction load | Interference fit | Interference fit | Cranks |
2) Effect of load magnitude
When a radial load is applied, the inner ring will expand slightly. Since this expansion enlarges the circumference of the bore minutely, the initial interference is reduced.
The reduction can be calculated by the following equations :
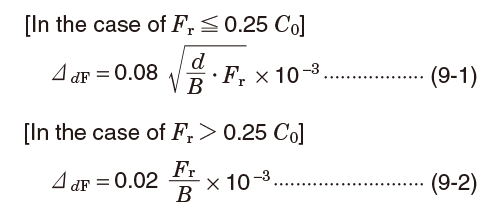
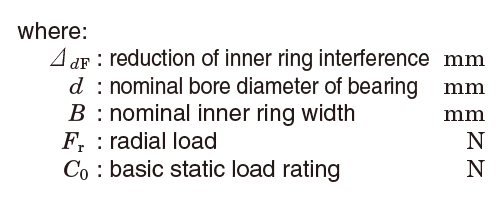
Consequently, when the radial load, exceeds the C0 value by more than 25 %, greater interference is needed.
Much greater interference is needed, when impact loads are expected.
Effect of fitting surface roughness
The effective interference obtained after fitting differs from calculated interference due to plastic deformation of the ring fitting surface. When the inner ring is fitted, the effective interference, subject to the effect of the fitting surface finish, can be approximated by the following equations :
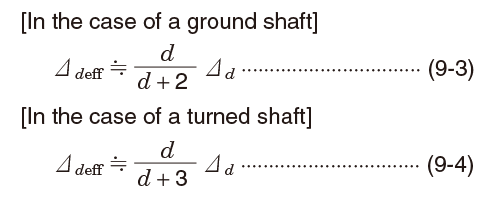
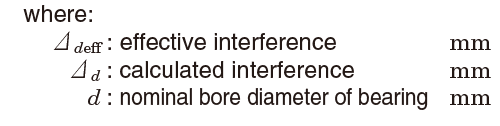
4) Effect of temperature
A bearing generally has an operating temperature, higher than the ambient temperature. When the inner ring operates under load, its temperature generally becomes higher than that of the shaft and the effective interference decreases due to the greater thermal expansion of the inner ring.
If the assumed temperature difference between the bearing inside and surrounding housing is Δt , the temperature difference at the fitting surfaces of the inner ring and shaft will be approximately (0.10 to 0.15) × Δt.
The reduction of interference (Δdt) due to temperature difference is then expressed as follows :

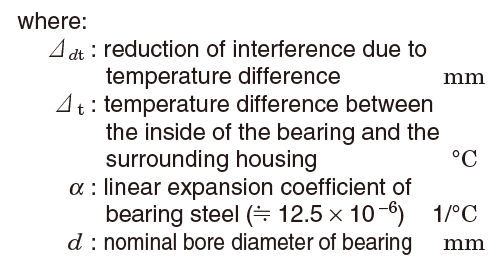
Consequently, when a bearing is higher in temperature than the shaft, greater interference is required.
However, a difference in temperature or in the coefficient of expansion may sometimes increase the interference between outer ring and housing. Therefore, when clearance is provided to accommodate shaft thermal expansion, care should be taken.
5) Maximum stress due to fit
When a bearing is fitted with interference, the bearing ring will expand or contract, generating internal stress.
Should this stress be excessive, the bearing ring may fracture.
The maximum bearing fitting-generated stress is determined by the equation in Table 9-2.
In general, to avoid fracture, it is best to adjust the maximum interference to less than 1/1 000 of the shaft diameter, or the maximum stress (σ), determined by the equation in Table 9-2, should be less than 120MPa.
Table 9-2 Maximum fitting-generated stress in bearings
Shaft & inner ring | Housing bore & outer ring |
---|---|
![]() |
![]() |
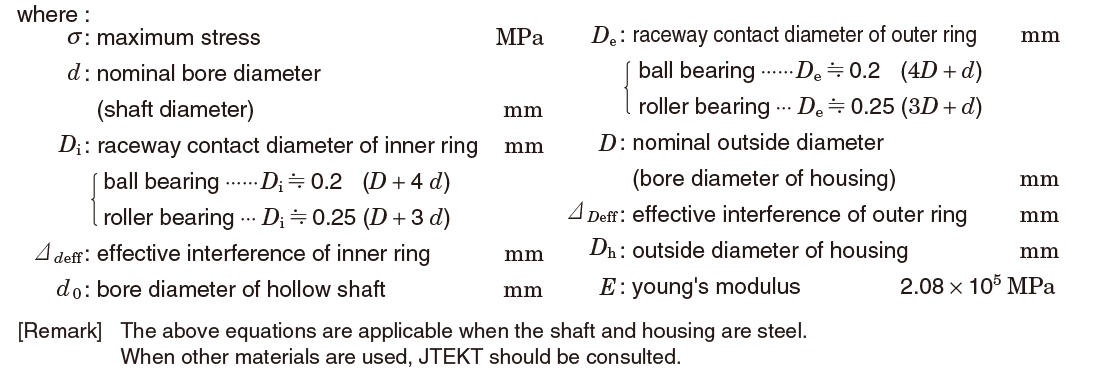
[Remark]The above equations are applicable when the shaft and housing are steel.
When other materials are used, JTEKT should be consulted.
6) Other considerations
When a high degree of accuracy is required, the tolerance of the shaft and housing must be improved. Since the housing is generally less easy to machine precisely than the shaft, it is advisable to use a clearance fit on the outer ring.
With hollow shafts or thin section housings, greater than normal interference is needed.
With split housings, on the other hand, smaller interference with outer ring is needed.
When the housing is made of aluminum or other light metal alloy, relatively greater than normal interference is needed. In such a case, consult with JTEKT.