5-2-1 基本動定格荷重 C
軸受の転がり疲れに対する強さすなわち負荷能力を表わす基本動定格荷重とは、内輪を回転させ外輪を静止させた(又は内輪を静止させ外輪を回転させた)条件で、100万回転の基本定格寿命が得られるような、大きさと方向が一定の純ラジアル荷重(ラジアル軸受の場合)又は中心アキシアル荷重(スラスト軸受の場合)をいう。それぞれ基本動ラジアル定格荷重(Cr)又は基本動アキシアル定格荷重(Ca)と呼び、これらの値を軸受寸法表に記載している。
5-2-2 基本定格寿命 L10
軸受の基本定格寿命L10は、軸受内部が標準設計され、JISで規定されるあるいはそれらに相当する軸受用鋼材で、高い製造品質で造られた軸受が、通常の使用条件で使用される信頼度90%の寿命である。軸受の基本動定格荷重、動等価荷重及び基本定格寿命の関係は、式(5-1)で表すことができる。
なお、この寿命計算式は、非常に大きな荷重条件(Pが、基本静定格荷重C0(参照:基本静定格荷重と静等価荷重)又は0.5Cのいずれかの値を超える場合)による軌道と転動体との接触面の塑性変形などの影響や、逆に非常に小さな荷重条件による軌道と転動体との接触面の滑りなどの影響がある場合は対象としない。
これらの条件が考えられる場合は、JTEKTにご相談下さい。
軸受が一定の回転速度で使用される場合には、式(5-2)に示すように寿命を時間で表した方が便利である。
また、鉄道車両や自動車などでは、式(5-3)で示すように寿命を走行距離(km)で表すことが多い。
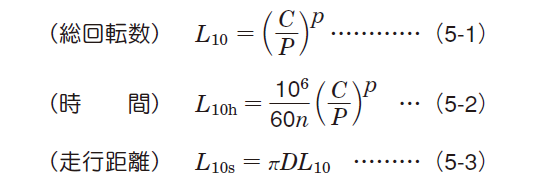
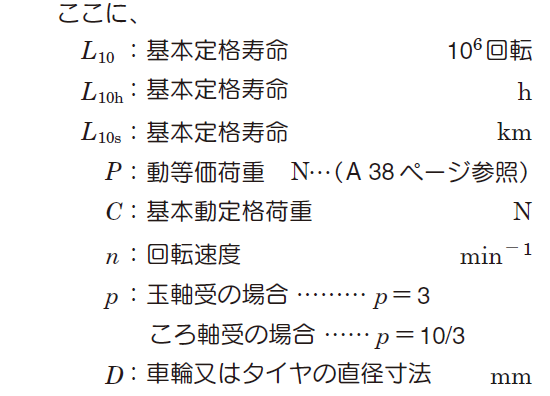
従って、 軸受の使用条件として、 動等価荷重をP、回転速度をnとすると、設計寿命を満たすのに必要な軸受の基本動定格荷重Cは式(5-4)で求められるので、このCを満足する軸受を軸受寸法表の中から選定することにより、軸受の寸法を決めることができる。
使用機械と軸受の必要寿命時間については、『表5-5 軸受の必要寿命時間』を参考にしてください。

参考
式(5-2)において、寿命係数(ƒh)及び速度係数(ƒn)を用いた計算式を次に示す。
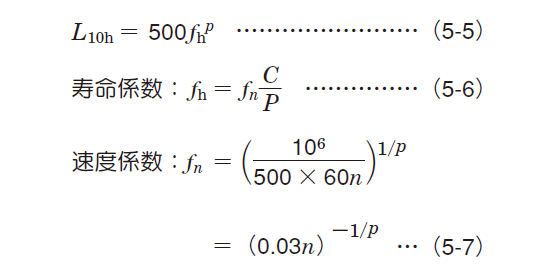
ƒn、ƒh及びL10hの値は〔参考図〕として記載したノモグラムを用いて簡易的に求めることができる。
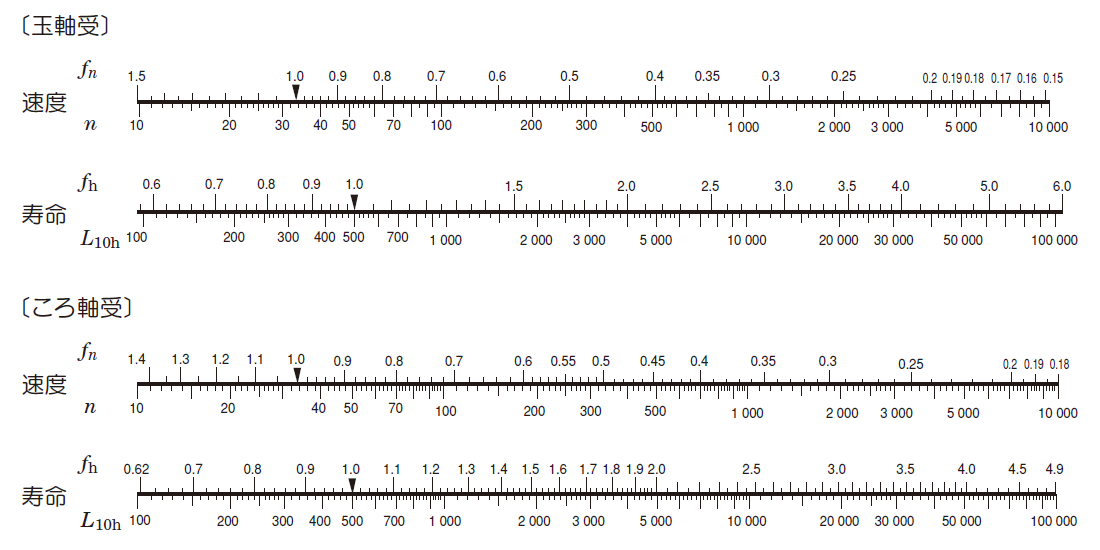
〔参考図〕回転速度(n)と速度係数(ƒn)及び寿命係数(ƒh)と寿命(L10h)
5-2-3 温度による基本動定格荷重の補正と寸法安定化処理軸受
軸受を高温で使用すると材料の組織が変化して硬さが低下し、常温で使用する場合より基本動定格荷重が減少する。一度材料の組織が変化すると、温度が常温に戻っても元へ戻らない。
従って、高温で使用する場合は、軸受寸法表に示した基本動定格荷重値に表5-1の温度係数を乗じて補正する必要がある。
表 5-1 温度係数の値
軸受温度,℃ | 125 | 150 | 175 | 200 | 250 |
---|---|---|---|---|---|
温度係数 | 1 | 1 | 0.95 | 0.90 | 0.75 |
軸受を120℃以上で長時間使用する場合、通常の熱処理では寸法変化量が大きくなるため、寸法安定化処理が必要となる。
寸法安定化処理した場合の記号と使用温度範囲を表5-2に示す。
ただし、寸法安定化処理を施した軸受は硬さが低くなるため、基本動定格荷重が減少する場合もある。
表 5-2 寸法安定化処理
寸法安定化処理記号 | 使用温度範囲 |
---|---|
S0 | 100℃を超え150℃以下 |
S1 | 150℃を超え200℃以下 |
S2 | 200℃を超え250℃以下 |
5-2-4 修正定格寿命 Lnm
転がり軸受の寿命は、基本定格寿命として1960年代に規格化されたが、実際にアプリケーションで使用した場合、潤滑状態、使用環境の影響により実寿命と基本定格寿命とが大きくかけ離れる場合があった。そこで、計算で求める寿命をより実寿命に近づけるため1980年頃から補正定格寿命として、軸受特性係数α2(軸受材料、製造工程、設計により寿命に関する特性が変化する場合の補正係数)及び使用条件係数α3(軸受寿命に直接影響する潤滑などの使用条件を考慮した補正係数)あるいはそれらは相互依存していることからまとめてα23係数として基本定格寿命に考慮する概念が検討された。これらの係数は、各軸受メーカが独自で対応していたが、2007年にISO 281で修正定格寿命として規格化され、2013年にJIS B 1518(動定格荷重及び定格寿命)が、ISOとの整合性を図るため改正された。
式(5-1)に示した基本定格寿命(L10)は、内部設計、材料、製造品質などが標準の転がり軸受において、通常使用条件での信頼度90%の(疲れ)寿命である。JIS B 1518:2013は、ISO 281:2007に基づき、さらに、様々な運転条件での正確な軸受寿命を求めるため、異なった信頼度並びにシステムアプローチとして各要因の変化や相互作用などの影響を、軸受内部の付加的応力として潤滑状態、潤滑剤の汚染及び疲労限荷重Cu(参照:(2)b 疲労限荷重 Cu)を考慮した計算方法を規定した。これらを考慮した寿命修正係数αISOを用いた寿命を修正定格寿命Lnmといい、式(5-8)で求められる。

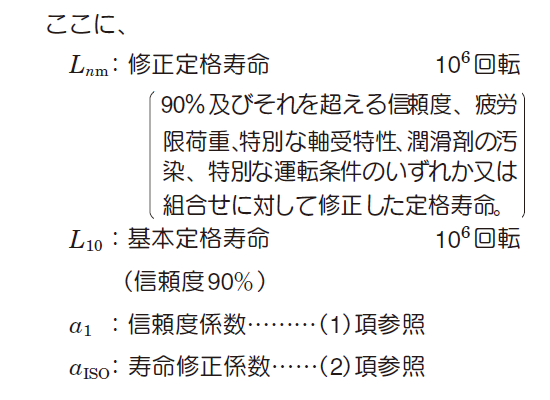
〔備考〕信頼度が90%を超えるLnmを用いて軸受寸法を選定する場合には、軸及びハウジングの強度などについても特に注意する必要がある。
(1) 信頼度係数 α1
信頼度は、"一群の同じ軸受を同一の条件で運転したとき、特定の寿命に達するか、又はそれを超えることが期待される軸受の個数の総個数に対する割合"で、信頼度が90%以上(破損確率が10%以下)の修正定格寿命を求める場合のα1の値を表5-3に示す。
表 5-3 信頼度係数 α1
信頼度,% | Lnm | α1 |
---|---|---|
90 | L10m | 1 |
95 | L5m | 0.64 |
96 | L4m | 0.55 |
97 | L3m | 0.47 |
98 | L2m | 0.37 |
99 | L1m | 0.25 |
99.2 | L0.8m | 0.22 |
99.4 | L0.6m | 0.19 |
99.6 | L0.4m | 0.16 |
99.8 | L0.2m | 0.12 |
99.9 | L0.1m | 0.093 |
99.92 | L0.08m | 0.087 |
99.94 | L0.06m | 0.080 |
99.95 | L0.05m | 0.077 |
(表5-3 JIS B 1518:2013 引用)
(2) 寿命修正係数 αISO
a)システムアプローチ
軸受寿命への様々な影響は、相互に依存している。修正寿命計算のシステムアプローチでは、寿命修正係数αISOを求めるための実用的な手法として評価する(図5-1参照)。寿命修正係数αISOは、式(5-9)で求められ、軸受形式(ラジアル玉軸受、ラジアルころ軸受、スラスト玉軸受、スラストころ軸受)ごとに以下の線図を用い求める。(図5-2、5-3、5-4及び5-5参照)
なお、実用上、寿命修正係数は、αISO≦50とする。

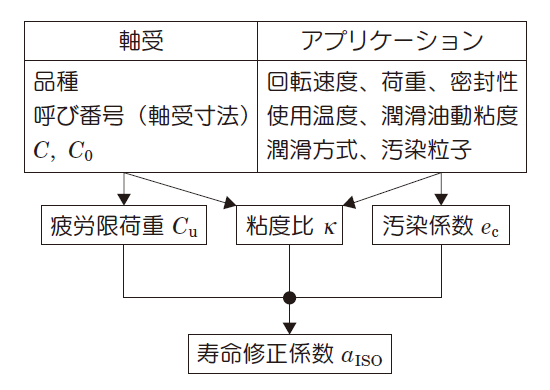
図 5-1 システムアプローチ
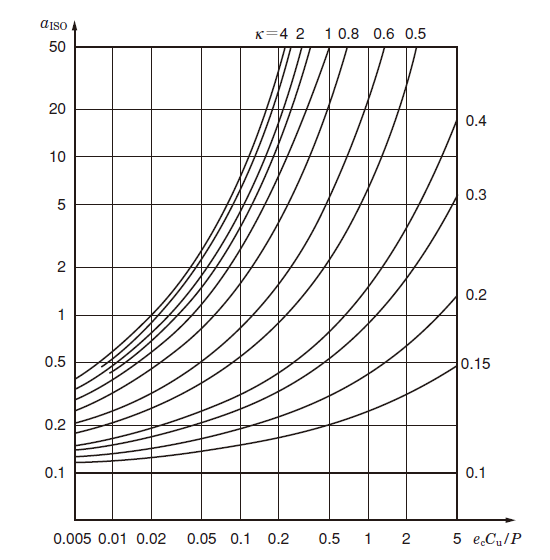
図 5-2 寿命修正係数 αISO(ラジアル玉軸受)
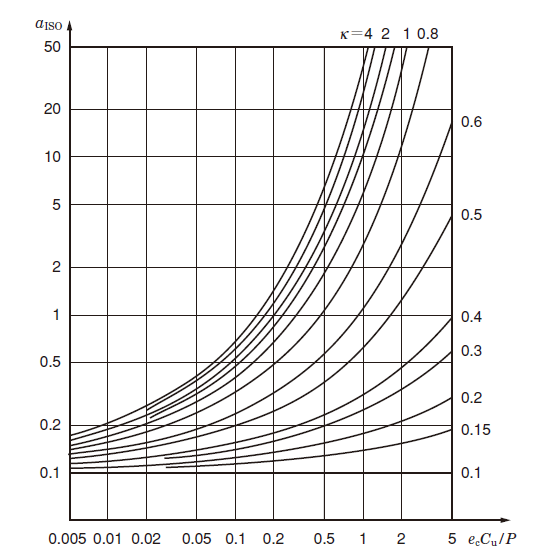
図 5-3 寿命修正係数 αISO(ラジアルころ軸受)
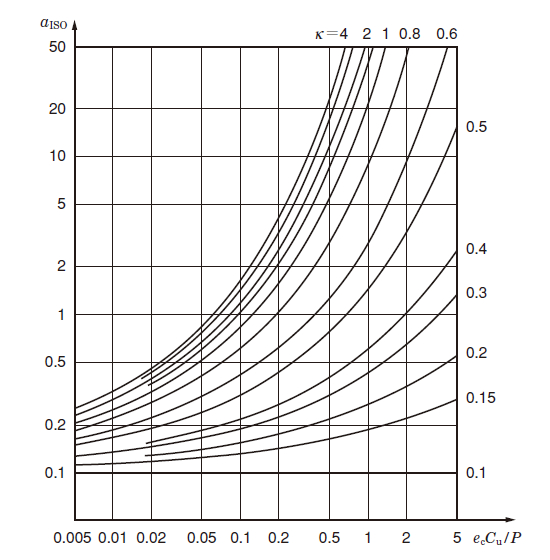
図 5-4 寿命修正係数 αISO(スラスト玉軸受)
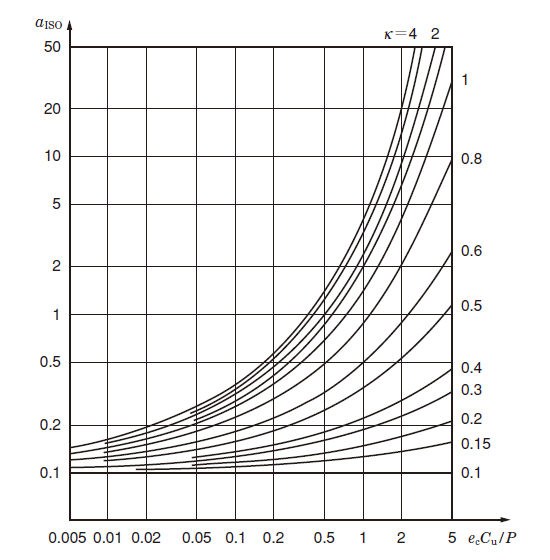
図 5-5 寿命修正係数 αISO(スラストころ軸受)
(図5-2~5-5 JIS B 1518:2013 引用)
b)疲労限荷重 Cu
規定鋼材又は同等品質の合金鋼は、潤滑条件、潤滑剤の清浄度及び他の運転条件が良好なら、ある荷重条件以下では疲れ寿命が無限となる。一般的な高品質の材料及び高い製造品質の軸受では、約1.5GPaの軌道面と転動体との接触応力のときに疲労限応力になる。材料品質及び/又は製造品質が低い場合には、疲労限応力は低くなる。
疲労限荷重Cuは、"軌道の最大荷重接触部で疲労限応力となる、軸受にかかる荷重"であり、軸受形式、大きさ、材料などに影響する。
なお、特殊軸受など本カタログに記載のない軸受の疲労限荷重は、 JTEKTにご相談下さい。
c)汚染係数 ec
汚染された潤滑剤の固体粒子が軌道面と転動体とで噛み込まれると、軌道面及び/又は転動体に圧こんが生じる場合がある。これらの圧こんで、局部的に応力が増加して、寿命が低下する。この潤滑剤の汚染による寿命低下は、汚染レベルから汚染係数ecとして求めることができる。
ここで、表中のDpwはピッチ径で、簡易的にDpw=(D+d)/2である。
なお、特殊な潤滑条件や詳細検討などは、JTEKTにご相談下さい。
表 5-4 汚染係数ecの値
汚染レベル | ec | |
---|---|---|
Dpw<100mm | Dpw≧100mm | |
極めて高い清浄度:粒子の大きさは潤滑剤の油膜厚さ程度で、実験室レベルの環境 | 1 | 1 |
高い清浄度:極めて細かなフィルタでろ過された油、標準的なグリース封入軸受及びシール軸受 | 0.8~0.6 | 0.9~0.8 |
標準清浄度:細かなフィルタでろ過された油、標準的なグリース封入軸受及びシールド軸受 | 0.6~0.5 | 0.8~0.6 |
軽度の汚染状態:潤滑剤が僅かに汚染 | 0.5~0.3 | 0.6~0.4 |
普通の汚染状態:シールなし、粗いフィルタ使用、摩耗粉及び周辺から粒子が侵入する環境 | 0.3~0.1 | 0.4~0.2 |
重度の汚染状態:著しく汚染された周辺環境かつ、軸受の密封性が不十分な状態 | 0.1~0 | 0.1~0 |
極度の汚染状態 | 0 | 0 |
(表5-4 JIS B 1518:2013 引用)
d)粘度比 κ
潤滑剤は、転がり接触表面に油膜を形成して軌道及び転動体を分離する。潤滑剤の油膜の状態は、基準動粘度ν1に対する運転時の動粘度νの比である粘度比κで表し、式(5-10)で求める。
κ>4の場合には、κ=4、κ< 0.1の場合には適用外とする。
なお、グリース潤滑や極圧添加剤入り潤滑剤などの場合は、JTEKTにご相談下さい。

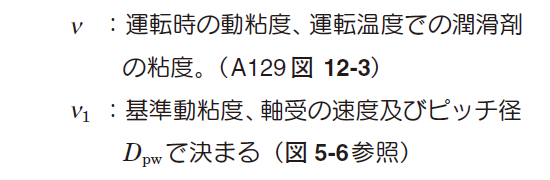
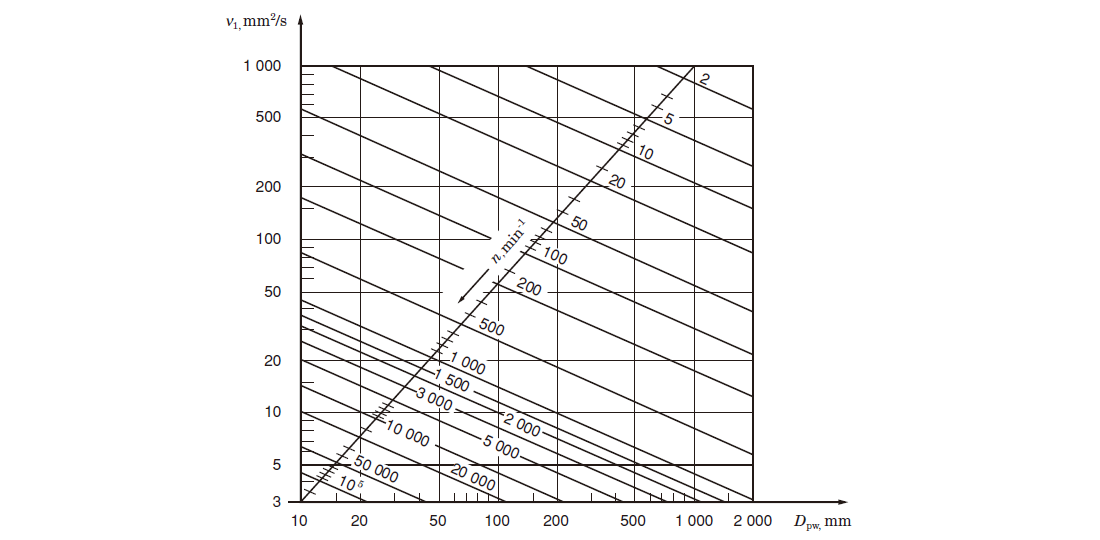
(図 5-6 JIS B 1518:2013 引用)
図 5-6 基準動粘度ν1
5-2-5 複数個の軸受のシステム寿命
2個以上の軸受を使用する装置においては、1個の軸受が破損しても、その装置の機能が停止してしまうようなことが多い。
使用している軸受全体を一つの軸受システムとみなすと、その軸受システムの定格寿命は次式で求められる。

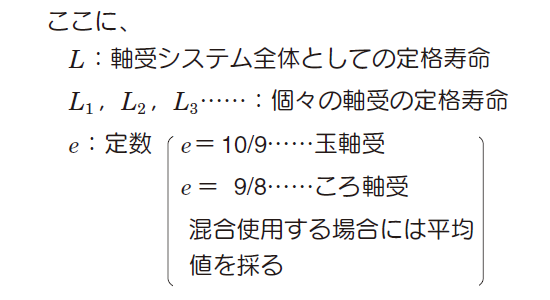
〔例〕
ある一つの軸が2個のころ軸受で支えられている場合を考え、一方の軸受が50000時間、他方の軸受が30000時間の定格寿命をもつものとすれば、この軸に使用されている軸受全体としての定格寿命は、式(5-11)より次のようになる。
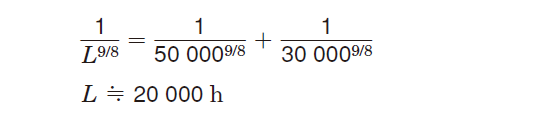
すなわち、軸受全体の定格寿命は、個々の軸受の短いほうの定格寿命よりも、短くなることが分かる。
この結論はきわめて重要であり、2個以上の軸受を使用する装置で、システムとしての軸受寿命を考える必要がある場合には、注意しなければならない。
5-2-6 使用機械と軸受の必要寿命時間
使用軸受の寿命をいたずらに長くすることは、必ずしも経済的ではない。使用機械や使用条件によって、その軸受の必要寿命を設定するのがよい。
表5-5に経験的に採用されている必要寿命時間を参考に示す。
表 5-5 軸受の必要寿命時間(参考)
使用条件 | 使用機械 | 必要寿命時間(h) |
---|---|---|
短時間、又は断続的に運転 | 家庭用電気器具・電動工具、農業機械、重量物巻上げ装置 | 4000~8000 |
常時使用しないが確実な運転 | 家庭冷暖房器用電動機、建設機械、コンベヤ、エレベータ | 8000~12000 |
不連続であるが長時間運転 | 圧延機ロールネック、小形電動機、クレーン | 8000~12000 |
工場電動機、一般歯車装置 | 12000~20000 | |
工作機械、振動スクリーン、クラッシャ | 20000~30000 | |
コンプレッサ、ポンプ、重要な歯車装置 | 40000~60000 | |
1日8h以上常時運転、又は連続で長時間運転 | エスカレータ | 12000~20000 |
遠心分離機、空調設備、送風機、木工機械、鉄道車両車軸 | 20000~30000 | |
大形電動機、鉱山ホイスト、車両用主電動機、機関車車軸 | 40000~60000 | |
製紙機械 | 100000~200000 | |
24h連続運転、故障が許されない | 水道設備、発電所設備、鉱山排水設備 | 100000~200000 |